Animation
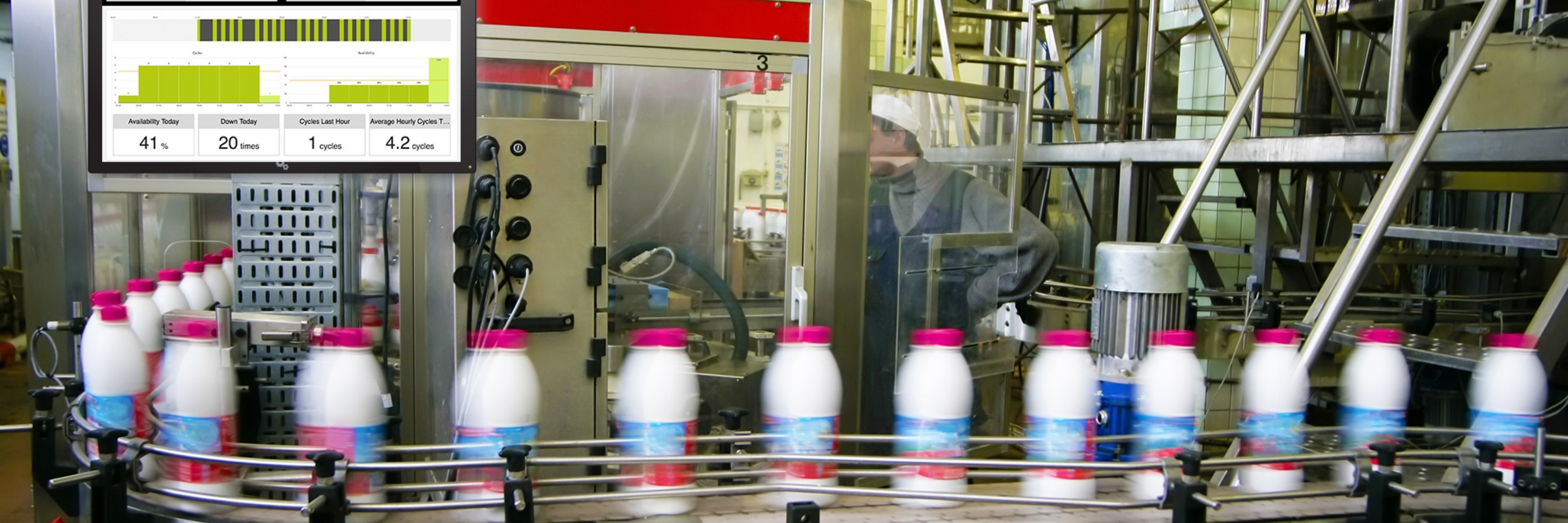
Here are some of the key takeaways you’ll receive from this guide:
Download now
What people are saying about this
Frequently asked questions
How fast can you deploy?
We typically require a 2 to 4 week lead time. Installation usually takes 1 hour per machine.
Which currencies do you support?
Based on your location, you have the option to pay in Canadian dollars, US dollars, or euros.
What are the payment options?
You can choose from a variety of subscription payment options - monthly billing or upfront payment via credit card, direct deposit, or check - for any package that suits your needs.
What are the subscriptions durations?
You can choose between monthly, 1-year and 3-year subscriptions.
Do you offer a trial period?
Yes, we offer a 30-day trial period. For further information, feel free to reach out to one of our experts.