In the competitive landscape of food and beverage manufacturing, implementing continuous improvement methodologies isn't just a choice—it's a necessity for staying ahead. Embracing a culture of continuous improvement ensures efficiency, quality, and ultimately, customer satisfaction. But what are the key tools that can drive this improvement forward? Let's delve into the pillars of continuous improvement and explore some effective tools tailored for the food and beverage industry.
The Pillars of Continuous Improvement
Understanding Continuous Improvement
Continuous improvement, often referred to as Kaizen, is a six sigma management practice centered around constantly seeking ways to enhance business processes, products, and services. It involves small, incremental improvements that cumulatively lead to significant efficiencies over time. In the context of food and beverage manufacturing, this means refining manufacturing processes, minimizing waste, and maximizing quality.
The Role of Continuous Improvement in Manufacturing
For food and beverage manufacturers, continuous improvement is more than just a productivity booster—it's a strategic imperative. It fosters innovation, ensures compliance with stringent regulations, and enables companies to stay ahead in a rapidly evolving market. By embracing a continuous improvement model, manufacturers can adapt to changing consumer preferences, streamline operations, and drive sustainable growth.
Identifying the Need for Improvement Tools
Common Challenges in Food and Beverage Manufacturing
Food and beverage manufacturers face a myriad of challenges, including stringent regulations, volatile raw material costs, fluctuating consumer demands, and intense competition. These challenges necessitate a proactive approach to problem-solving and optimization to stay relevant and profitable in the industry. Root cause analysis, combined with six sigma methodologies like the DMAIC and PDCA cycle (plan-do-check-act), helps in identifying improvement opportunities and implementing targeted solutions for lasting improvements.
The Importance of Root Cause Analysis
Effective problem-solving begins with identifying the root causes of issues rather than just addressing symptoms. Root cause analysis enables manufacturers to pinpoint underlying issues, whether it's inefficiencies in production processes, equipment failures, or quality control issues. By addressing these root causes, companies can implement targeted solutions that yield measurable results.
Our Top Three Strategies for Improvement
In our exploration of continuous improvement tools, three stand out as essential for lean manufacturing: Catchball, Gemba Walks, and Hoshin Kanri.
Catchball
Catchball is based on a simple premise: The more individuals who tackle a problem, the better the solution will be. Catchball formalizes this shared responsibility without complicating matters by having too many people working at once.
When a continuous improvement project is started, those involved create a clear blueprint, complete with background information, pain points, objectives, and metrics. Because it is so comprehensive and easily understood, the blueprint serves as instructions for anyone involved throughout project management, and it can be transferred from leader to leader until it is complete—the same way you would pass a ball in sports.
Here, the project—and its corresponding needs and instructions—gets passed to the best team to move it forward at a given stage. The goal is to move projects through to completion by always handing them to the most qualified team members, preventing the lag time that would otherwise happen if the project wound up in inexperienced hands.
Gemba Walks
“The real place.” That’s what “gemba” means in Japanese. In practice, Gemba Walks give managers a real picture of their operations. It sounds fancy, but it’s really just a strategy in which managers and supervisors travel to plants with one goal in mind: to observe their frontline operations and find opportunities for improvement.
These walkthroughs bring workers and supervisors together, fostering face-to-face interaction with the experts who run the daily factory operations. And it opens the door to new perspectives for people who have become accustomed to set strategies. By finding and responding to various inefficiencies with new methods, you can limit your capital loss over time.
However, you can’t go into Gemba Walks halfheartedly; they need a plan supporting them. To make these walkthroughs effective as continuous improvement tools, scatter your activities. Visit the plant on different days of the week, during different hours. No two days or shifts are alike, and worker behavior changes, so the scatter approach presents a more accurate picture of your operations.
It is also important to let your frontline take the lead, rather than stepping in with complex questions and comments. Leave your assumptions behind, and you’ll receive honest and accurate information from the team, fostering better relations and innovation.
Hoshin Kanri
We borrow another moniker from the Japanese—Hoshin Kanri, which loosely translates to “strategy deployment” or “direction management”—to guide improvement efforts on the factory floor. Hoshin Kanri is a formalized system of company alignment, with the goal of long-term success. The strategy relies on four principles:
- The whole organization must buy into a few well-defined goals.
- Objectives and strategies must be well communicated and universal throughout the company.
- Leadership must actively participate in fostering and creating improved processes.
- Lower-level employees must also embrace and work toward company objectives.
Hoshin Kanri and its associated principles aren't as strict as they seem. The guideposts are meant to foster creativity and communication throughout the hierarchy of your company, setting issues of seniority aside.
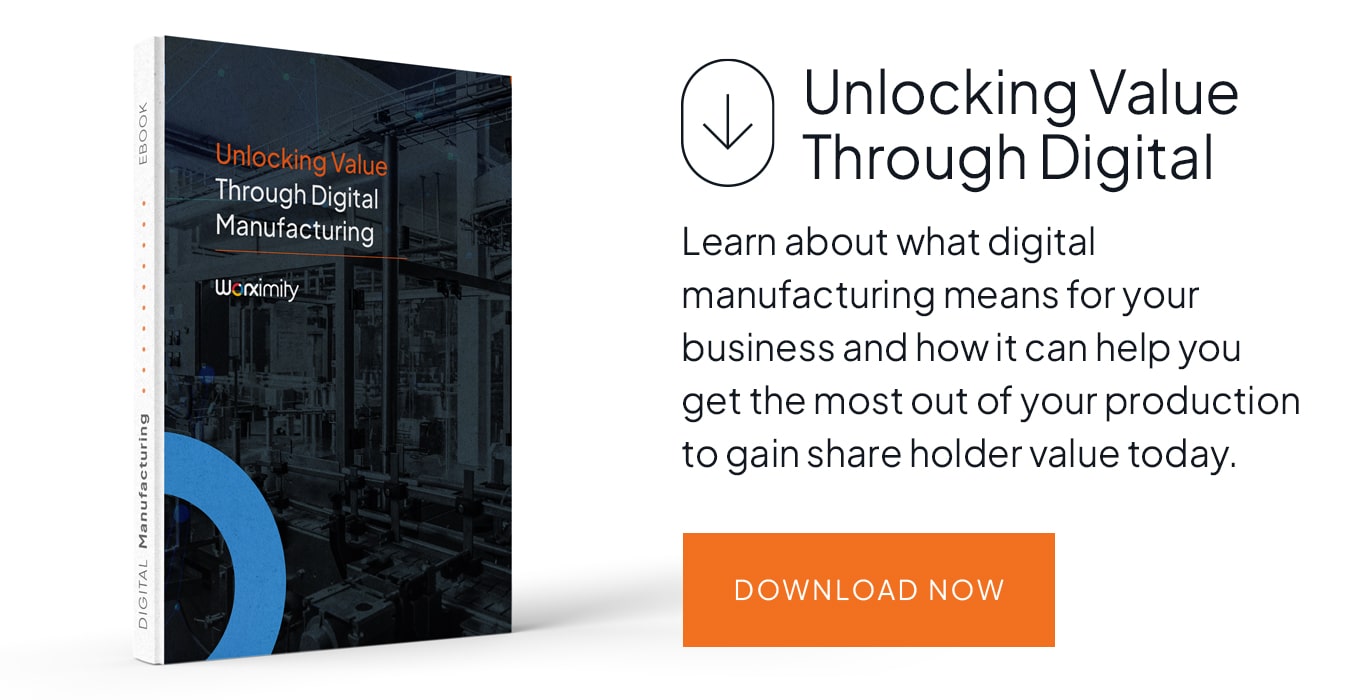
Continuous Improvement With Worximity
Leveraging Technology for Lean Management
Technology plays a pivotal role in lean management, enabling manufacturers to eliminate waste and drive continuous improvement. Worximity's solutions integrate seamlessly with existing systems, providing real-time insights into production metrics, inventory levels, and equipment performance.
Advanced Analytics for Decision Making
In an industry where margins are tight and competition is fierce, data-driven decision-making is paramount. Worximity's advanced analytics empower manufacturers to make informed decisions, whether it's optimizing production schedules, predicting maintenance needs, or identifying opportunities for cost savings.
Workflow Optimization and Process Improvement
Worximity offers tools specifically designed to optimize workflows and streamline processes in food and beverage manufacturing. By leveraging real-time data and analytics, manufacturers can identify bottlenecks, minimize downtime, and maximize operational efficiency.
Integration into Existing Systems
One of the key challenges in implementing continuous improvement tools is integration with existing systems. Worximity understands this challenge and offers solutions that seamlessly integrate with ERP systems, and other critical manufacturing technologies.
Training and Adoption
Successful implementation of continuous improvement tools hinges on effective training and adoption strategies. Worximity provides a comprehensive training program and ongoing support to ensure that users are equipped with the knowledge and skills needed to leverage these tools effectively.
Case Studies and Success Stories
Worximity has a proven track record of helping food and beverage manufacturers achieve tangible results through continuous improvement. From reducing downtime and waste to improving overall equipment effectiveness (OEE) and increasing profitability, Worximity's solutions have delivered measurable benefits across a wide range of manufacturing environments. Check out our success stories to learn more.
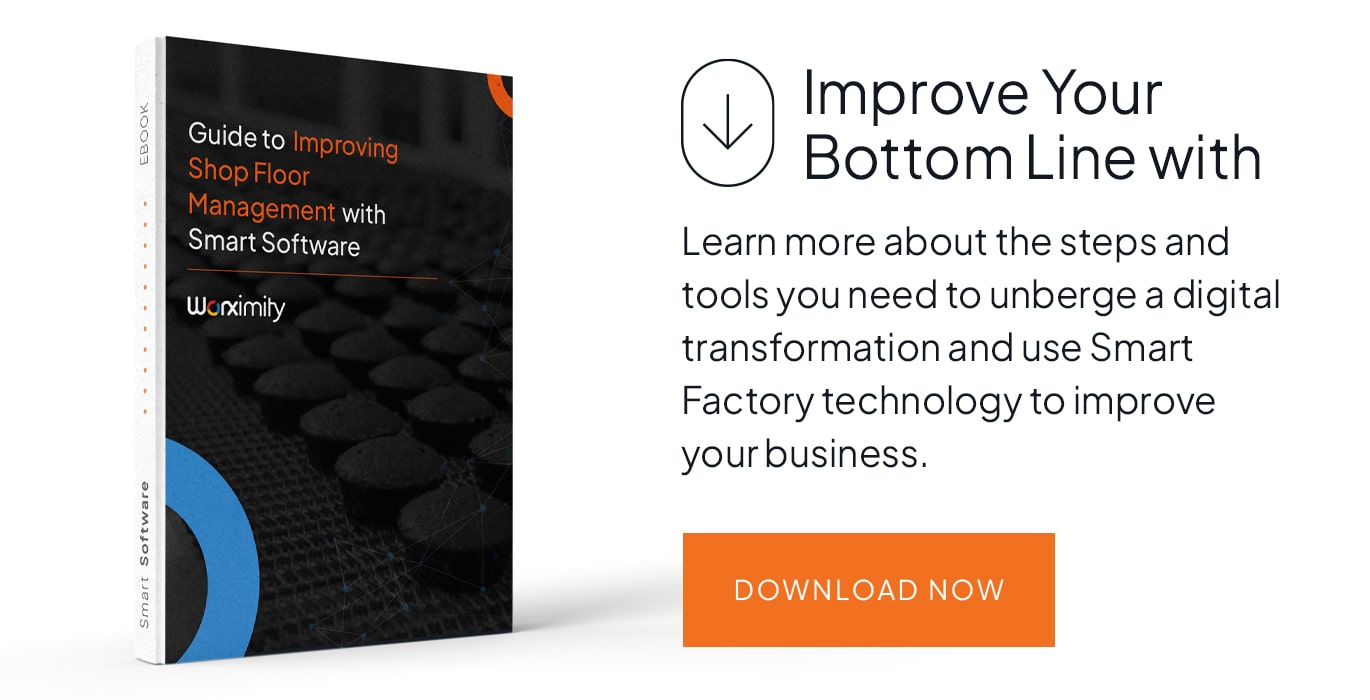