Food & Beverages Processing
Empowering food and beverage manufacturers with data that works.
Worximity provides food and beverage manufacturers with the data and insights they need to fine tune production and improve the efficiency of their machines and people— helping them get more done with what they already have.

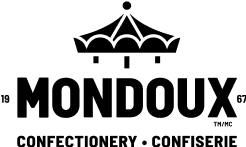
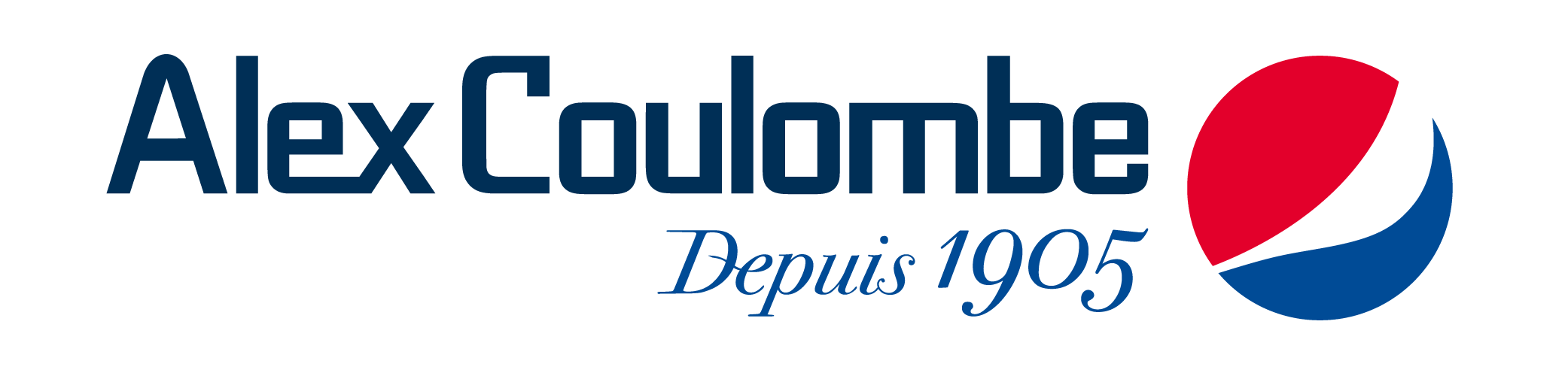
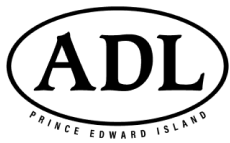
Why worximity
Unparalleled experience with over 100 clients in food and beverage.
Meat and poultry, dairy processors, beer and spirit producers, bakeries—we help a variety of food and beverage manufacturers get more done with what they already have.
Stabilize production costs.
Set and achieve targets that help ensure consistent production and costs.
Minimize waste.
Track everything from excess giveaway to yield.
Improve labour efficiency.
Put your team to work at the right time, on the right production lines.
Facilitate action.
Empower your team with the knowledge and processes they need to improve performance.
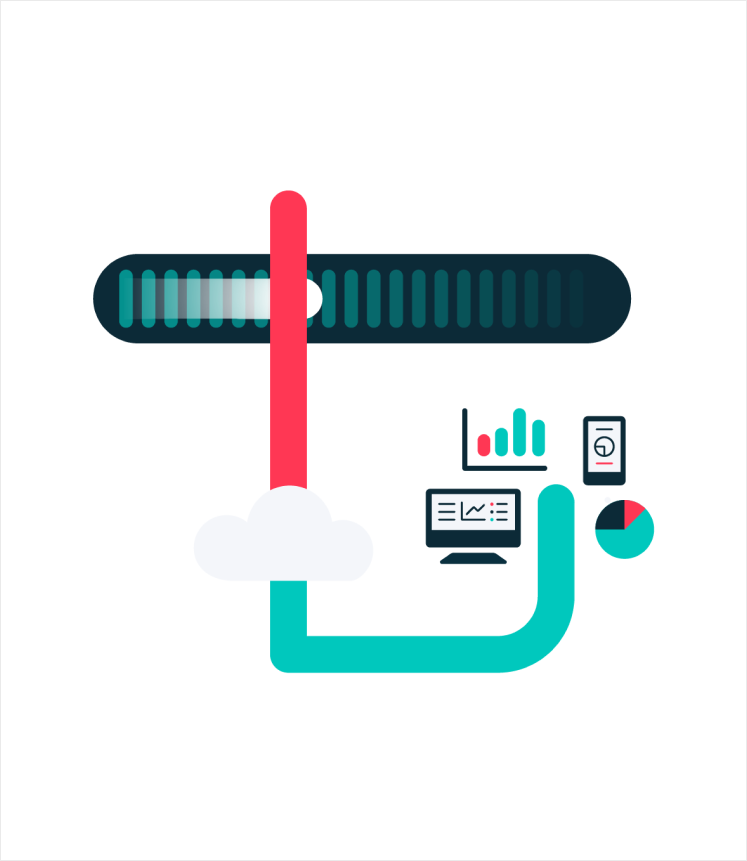
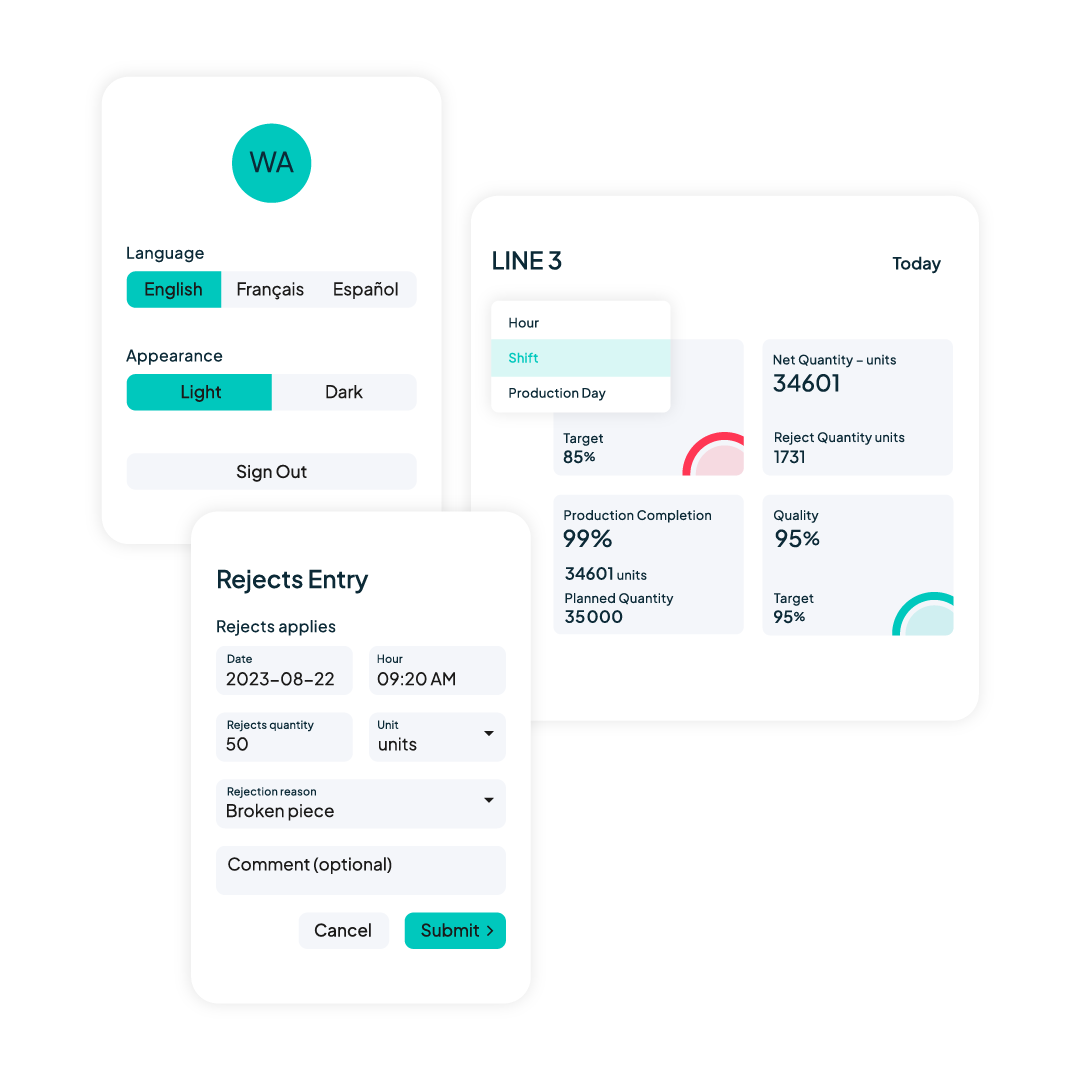
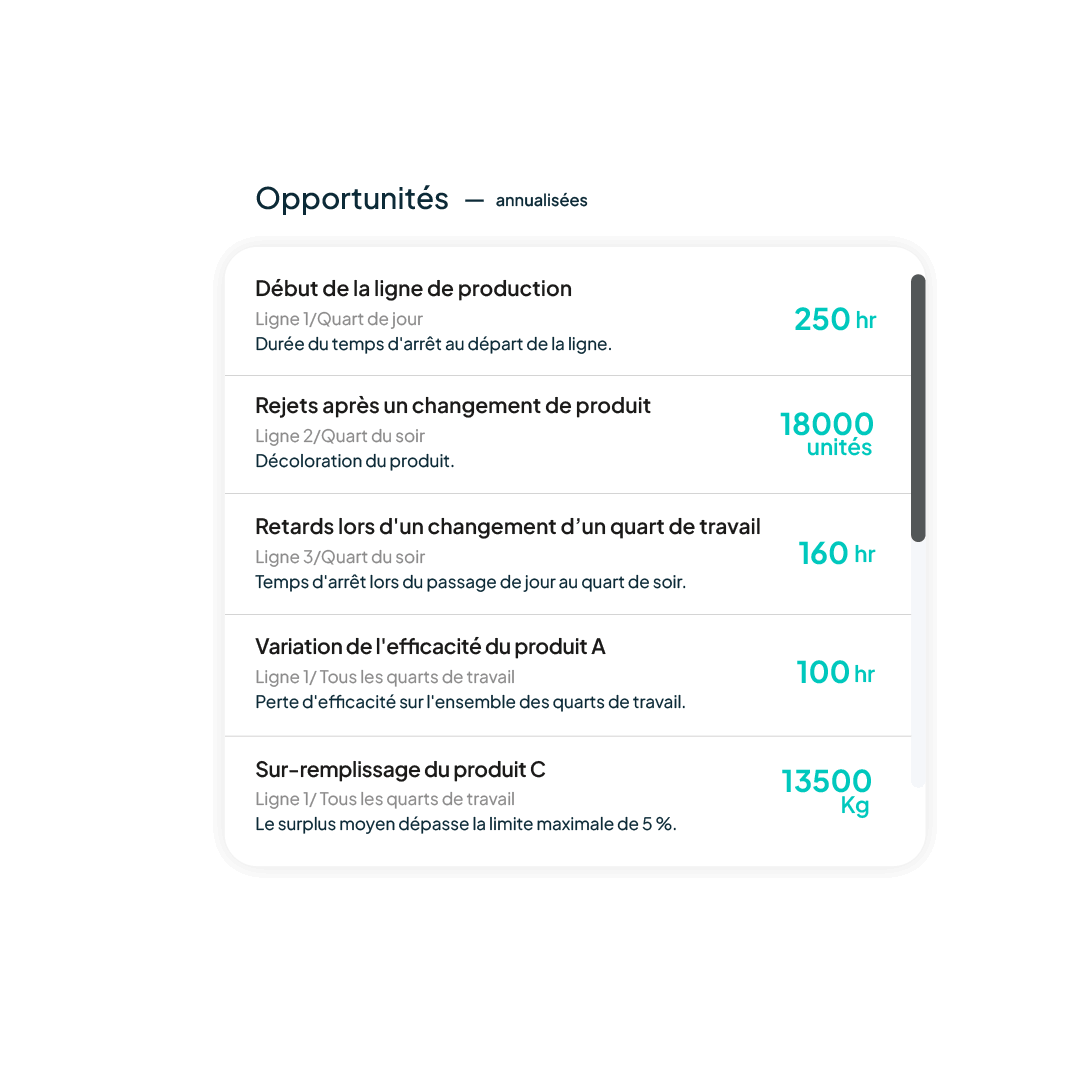
Connect any machine or production process
Manufacturing data acquisition solutions for any operation and budget.
Monitor Production. Improve Performance.
Effortlessly measure and improve OEE, throughput, downtime, and so much more.
Uncover your opportunities for improvement
Manufacturing analytics that clearly identify and prioritize your opportunities for improvement.
CAse study
How Worximity helped Première Moisson gain 27% in responsiveness in bakery factory
How the baking industry continues to grow with IIoT